Steels.
AUSTENITIC. MARTENSITIC. FERRIC.
AUSTENITIC.
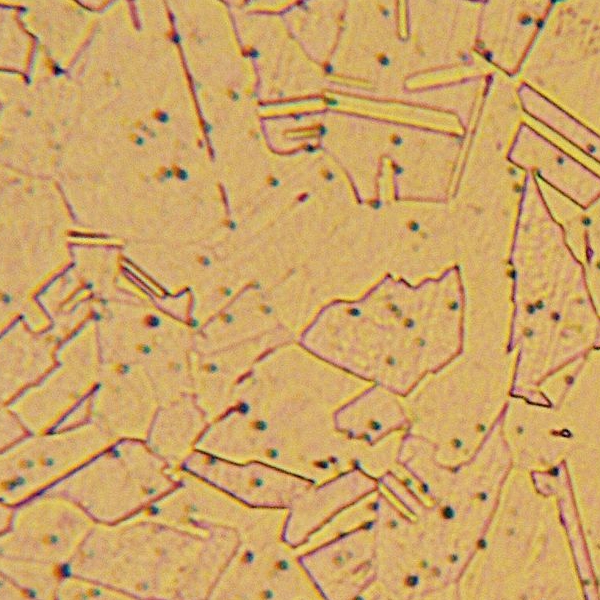
Austenitic stainless steels are formed from an iron-carbon-chromium-nickel alloy with the addition of any other elements such as molybdenum, titanium, niobium, etc.
Austenitic steels contain amounts of carbon ranging between lower values of 0.03 and values in the order of 0.25 per cent, chromium between 17 and 26 per cent and nickel between 7 and 22 per cent.
Increasing the nickel content improves machinability by plastic deformation. The mechanical properties at room temperature are good and at very low temperatures very good, especially the resilience, as well as high fatigue strength with low notch sensitivity.
The most used types of austenitic steels include:
AISI 304 is certainly the most widely used and marketed in the most common uses.
AISI 316 differs from 304 due to the addition of molybdenum, which allows an increase in resistance to pitting and stress corrosion. Used in marine sectors or with the presence of corrosive substances.
AISI 303, a variant of 304 with the addition of sulphur which gives improved machinability, particularly suitable for lathe processing.
MARTENSITICS.
Martensitic stainless steels are characterised by the predominant presence of chromium (approximately 11-19%) with the presence of other small quantities of alloys such as nickel for example. Carbon contents may vary from 0.08 to 1.20%.
Martensitic steels can increase their mechanical characteristics of strength and hardness by quenching heat treatment.
The most commonly used types of martensitic stainless steels include:
AISI 420, in its variants, is a steel that after suitable heat treatment (hardening and tempering) reaches fairly high hardness values, in addition to good characteristics of toughness and corrosion resistance. It is widely used for the following: knives, gears, surgical instruments, mechanical keys, etc.
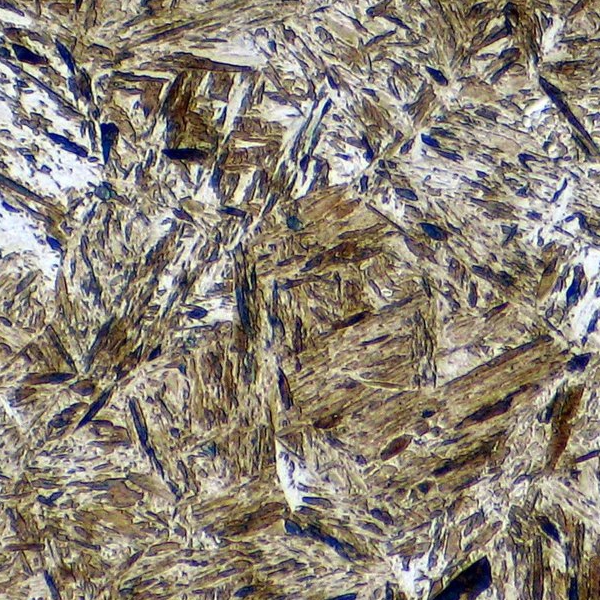
FERRITIC.
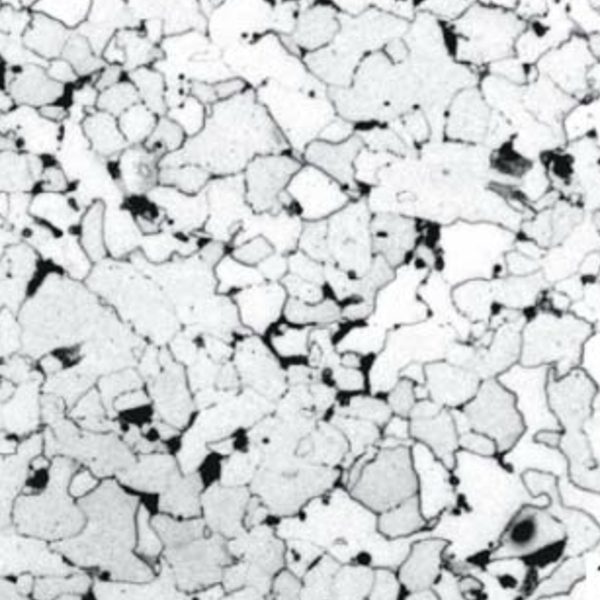
Ferritic stainless steels are iron-chromium-carbon alloys, possibly with slight additions of other elements such as molybdenum. Mechanical properties can be raised by cold deformation (wire drawing, rolling, etc.) to generate a phenomenon called ‘work hardening’.
The most commonly used types of ferritic stainless steels include:
AISI 430, with approximately 17% chromium, is undoubtedly the most widely used. It is easily usable in cold-working, has good corrosion resistance characteristics and is mainly used in the automotive and electric appliance industry.
STEELS TABLE.
CHEMICAL COMPOSITION (% values) |
AISI 409 | AISI 410S | AISI 420 | AISI 430 | AISI 303 | AISI 304 | AISI 321 | AISI 309S | AISI 310S | AISI 316L |
---|---|---|---|---|---|---|---|---|---|---|
Carbon – C | ≤ 0,03 | ≤ 0,08 | 0,26 0,35 |
≤ 0,08 | ≤ 0,10 | ≤ 0,07 ≤ 0,03L |
≤ 0,08 | ≤ 0,15 | ≤ 0,10 | ≤ 0,03 |
Manganese max – Mn | 1 | 1 | 1,5 | 1 | 2 | 2 | 2 | 2 | 2 | 2 |
Silicon max – Si | 1 | 1 | 1 | 1 | 1 | 1 | 1 | 1 | 1,5 | 1 |
Phosphorus max – P | 0,04 | 0,04 | 0,04 | 0,04 | 0,045 | 0,045 | 0,045 | 0,045 | 0,045 | 0,045 |
Sulphur max – S | 0,015 | 0,015 | 0,015 | 0,015 | 0,35 | 0,015 | 0,015 | 0,015 | 0,015 | 0,015 |
Chromium – Cr | 10,5 12,5 |
12 14 |
12 14 |
16 18 |
17 19 |
17 19,5 |
17 19 |
22 24 |
24 26 |
16,5 18,5 |
Nickel – Ni | – | 8 10,5 |
– | – | 8 10 |
8 10,5 |
9 12 |
12 14 |
19 22 |
10 13 |
Molybdenum – Mo | – | – | – | – | – | – | – | – | – | 2 2,5 |
Copper max – Cu | – | – | – | – | 1 | – | – | – | – | – |
Titanium – Ti | – | 0,65 | – | – | – | – | 0,7 | – | – | – |